Automation
Factors to Consider When Selecting a Pneumatic Cylinder for Your Automation Needs
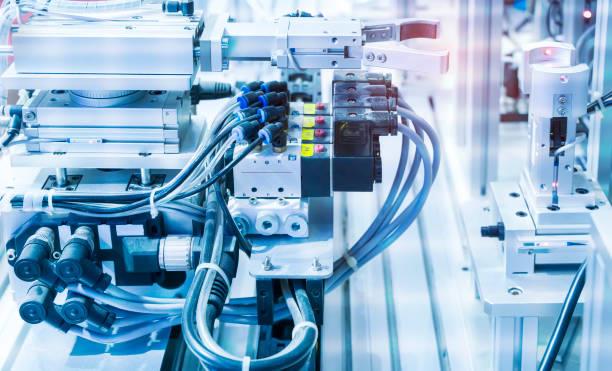
Pneumatic cylinders are needed for the movement and are vital devices in industrial automation. This lets you choose motion with stress that is efficient and accurate. Picking a pneumatic cylinder is important because it affects how well the system performs, and there are numerous factors that must be taken into account to make your choice. This is where the knowledge of an industrial automation distributor comes into play and can prove very helpful. Let’s look at the primary considerations when choosing a pneumatic cylinder for your automation system.
Establishing Your Automation Criteria
The first step towards selecting an appropriate pneumatic cylinder is having a rational assessment of your automation criteria. These requirements can differ considerably based on the nature of the process being automated. Whether you are performing light or heavy work, having knowledge of force and movement needs is extremely important. For example, the load and force capacity for the cylinder must be appropriate for the specific tasks. Stroke length and travel speed are also important; an application requiring slow, accurate movements will need a different type of cylinder than one that needs fast repetitive motions. Another factor to know is the type of force needed, which can be push or pull. This will influence the selection of the cylinder. Furthermore, some environmental factors such as temperature, humidity, and cleanliness should be considered in selecting a suitable pneumatic cylinder for your system. Consulting with manufacturers of the pneumatic cylinders and a distributor of industrial automation will guarantee that the cylinder selected answers the specification of your operation and application. Also, selecting the ideal cylinder ensures minimal downtimes, which greatly reduces the cost of maintenance and repairs.
Environmental Conditions and Durability
Factors such as temperature, level of moisture, and even exposure to chemicals contribute directly toward the overall selection of a pneumatic cylinder. Industrial and manufacturing settings are rife with particular difficulties such as high levels of heat, moisture, chemicals, and dust, all of which can be abrasive to an environment. Thus, it is imperative to choose a cylinder that guarantees the ability to survive such levels of demands, and ensures that the organization’s equipment can withstand the test of time. For instance: Food processing facilities use cylinders that should be made with materials that can withstand corrosion, similarly, high temperature settings must utilize materials that are extremely potent toward handling heat. Additionally, severe moisture, dust like particles and extreme chemicals demand the utilization of specialized coatings and seals. Furthermore, the smooth application of the cylinder in critical temperature ranges is a vital consideration for industries operating in cold or heat-sensitive areas. The perfect outfitting of an industrial automation distributor’s pneumatic cylinder with appropriate seals, coverings, and materials does the trick to match the requirements of durability. This tends to minimize the effort needed in maintenance, while also eliminating the chances of a breakdown in the system. Thus, allowing the organization to be more productive. It is possible to meet such environmental needs without sacrificing efficiency thanks to proper material science and cylinder performance experts.
Types and Configurations of Cylinders
Every single variety of pneumatic cylinder is designed differently in terms of shape and task automation. For most tasks the recommended option is a single acting cylinder where movement is only needed in one direction, while the returning motion in most cases is provided by a spring or external force. These are common in n bounded situations where the load would not have to go back to the set position under predetermined conditions. On the contrary, motion is possible in both directions for double acting cylinders making them useful for more controlled complicated tasks. Often in highly controlled settings that require a double action – pushing and pulling, double acting cylinders are more pragmatic. And for applications that require rotary instead of straight lined movement, rotary actuators come in handy. They aid in providing constant or periodic circular movement, primarily for machines that need to rotate parts or for opening and closing valves. Depending on your automation system requirements, your distributor will best recommend the correct shaped cylinder configuration that will improve the efficiency and functionality of your machinery. Additionally rod or without rod and compact cylinders should be included for mounting possibilities to meet space and flexible performance requirements.
Taking time to closely assess these options, helps ensure that your automation system works smoothly, while reducing the chances of faults.
Efficiency And Energy Utilization
The efficiency of an item is often a rounding concern for people, so retaining energy is something I take into consideration with a pneumatic cylinder as well. The reason for this is because, in large industrial applications, even small inefficiencies in the pneumatic system can lead to dire economic issues over time. As long as the proper seals or built in air cushioning are provided, advanced alterations allow seal systems to work more efficiently with less energy therefore, having longer cycle times. Installations of energy-efficient cylinders mitigate the compressors ability to cool air which hinders the level of automation in your system. Lowering the amount of air that is cooled also contributes to sustainability and less environmental impact. Working with arm efficient pneumatic cylinder manufacturers will help with satisfying your harsh automation demand without spending huge sums of money, leading to increased savings in the future. Fewer repairs or maintenance would be needed, allowing far more cost efficiency combined with the ability to use water freely.
Conclusion
During the selection of a pneumatic cylinder for an automation system, the load capacity, stroke length, environmental conditions, and energy consumption have to be evaluated. In order to choose the correct product, it is necessary to get guidance from pneumatic cylinder manufacturers, therefore, working with an industrial automation distributor helps for gaining good understanding with these manufacturers. Such collaboration means that the automation system performs efficiently, dependably, and economically. Considering the environmental conditions, types of cylinders, and energy used, aids in improving the performance and durability of the automation system and reduces operating expenses. In addition, routine work with care for monitoring helps in prolonging the life of the equipment and systems, making sure the operations are effective and efficient.
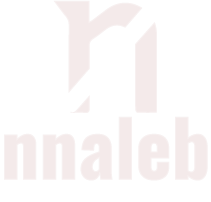
Automation
Best Automation Testing Tools for Startups
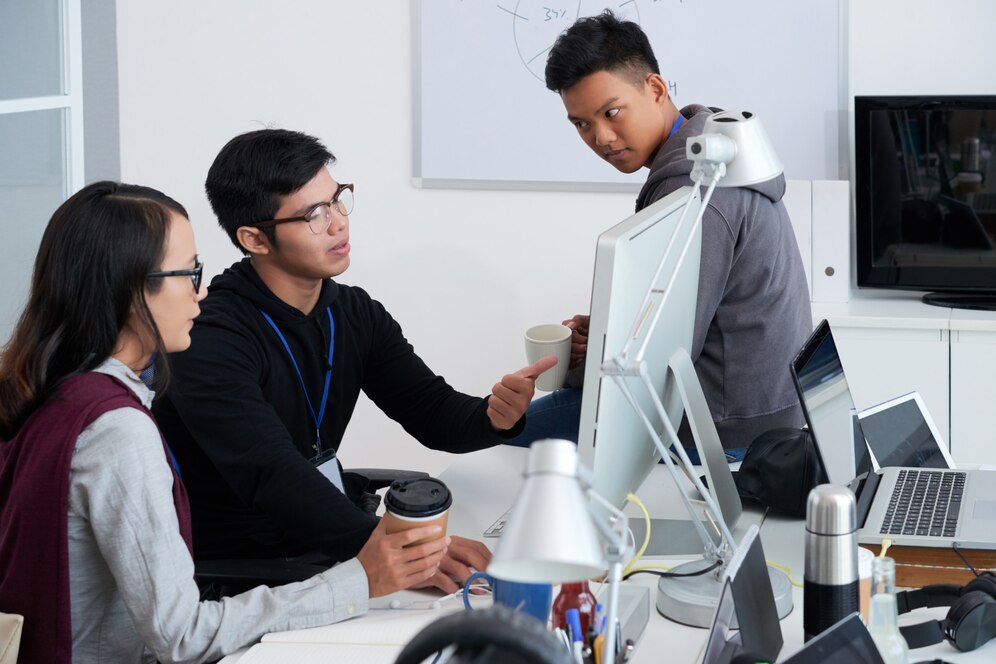
Startups operate in a high-pressure world where speed matters. They must ship products fast to keep up with demand. At the same time, quality cannot slip, or customers will leave. This balance is tough for small teams with limited budgets. Automation testing tools step in here to help. These solutions catch bugs early and ensure the product works well. Startups can save time and avoid hiring large QA teams.
Testing manually takes effort and slows everything down. Automation makes it quicker and more reliable. Small teams can run tests often without extra staff. This cuts costs and keeps the focus on building new features. Many startups turn to these tools for their simplicity and efficiency. The right choice can fit a tight budget while delivering solid results.
This blog post covers automation testing tools perfect for startups. Each one is affordable or free and easy to use. Small teams can adopt them without steep learning curves.
Top Automation Testing Tools for Startup Teams
Startups need automation testing tools that adapt to their needs. These solutions must be quick to set up and simple to run. They should also scale as the company grows. The tools below fit these criteria. Many are open-source or have free versions, keeping costs low for small teams.
LambdaTest
LambdaTest is one of the most widely used automation testing platforms today. It is an AI-native test execution platform that helps you run tests faster and speed up your release cycle.
Key Features
- It offers a large cloud infrastructure with support for 3000+ browsers and 10,000+ real device combinations.
- This helps you do cross-browser and cross-device testing with ease.
- You do not need to maintain physical testing devices.
- The platform gives you a scalable cloud environment. This saves you from hardware setup and maintenance.
- LambdaTest allows parallel testing, which cuts down testing time.
- It integrates with tools like Selenium, Cypress, Appium, Playwright, and others. This makes it easier to move your existing tests to the cloud.
- Another key feature is HyperExecute. It is an AI-native, end-to-end test orchestration platform. It improves the speed and efficiency of your automation testing.
Playwright
It is an open-source testing tool by Microsoft. It is great for cross-browser, mobile emulation, and parallel execution.
- Browser Support: Playwright works with Chromium, Firefox, and WebKit to test apps across different browsers. Startups can ensure their product looks good everywhere.
- Mobile Testing: It emulates mobile devices so teams can check how apps behave on phones or tablets. This helps catch issues early.
- Speed Boost: Parallel execution runs multiple tests at once, cutting down wait times. Teams get feedback faster and fix bugs sooner.
- Smart Waits: Auto-wait features handle dynamic content without extra coding. This saves effort for small teams with limited resources.
- Network Tools: It intercepts network calls to test APIs or mock responses. Startups can verify backend integration without complex setups.
Cypress
It is a fast, developer-friendly UI testing tool tailored for modern JavaScript apps.
- Real-Time Testing: Cypress runs tests in the browser for instant feedback. Developers spot issues as they code and fix them quickly.
- Easy Setup: Its simple API lets teams write tests without much training. Startups with new hires can get started fast.
- Auto Waits: It waits for elements automatically, skipping manual delays. This keeps tests smooth and reduces errors for beginners.
- Reporting: A built-in dashboard tracks test results and trends. Small teams can monitor quality without extra tools.
- Versatility: It handles end-to-end, integration, and unit tests in one package. Startups save time by using a single solution.
When people compare automation testing tools, “playwright vs cypress” often comes up. Both shine in different areas, like browser support or JavaScript focus.
Selenium
It is one of the most widely-used open-source frameworks supporting multiple languages and browsers.
- Language Options: Selenium supports Java, Python, C#, and more. Teams can use their preferred coding skills without switching.
- Browser Coverage: It tests on Chrome, Firefox, Safari, and Edge. Startups ensure their app works for all users.
- Distributed Testing: It runs tests across multiple machines for speed. This helps small teams handle big projects.
- CI/CD Fit: Selenium plugs into continuous integration pipelines. Startups can automate testing with every code push.
- Community Help: A large user base offers guides and forums. New teams find answers fast without paid support.
Appium
It is an open-source mobile automation framework for native, hybrid, and mobile web apps.
- Familiar Protocol: Appium uses WebDriver, known to Selenium users. Teams with web experience can jump in easily.
- Language Choices: It supports Java, Python, JavaScript, and others. Startups pick what fits their stack best.
- Device Flexibility: It tests on real devices, emulators, and simulators. Teams verify apps on various setups.
- Parallel Runs: Appium executes tests side by side to save time. Small teams get results quicker.
- Cloud Integration: It works with cloud testing platforms for broader coverage. Startups scale testing without buying hardware.
Cloud testing platforms give startups access to many devices and browsers. This cuts costs and boosts flexibility.
Puppeteer
It is a headless browser automation tool maintained by Google, ideal for Chrome-based app testing.
- Simple Control: Puppeteer offers an API to manage headless Chrome. Teams automate tasks with minimal code.
- UI Testing: It handles form submissions and clicks for quick checks. Startups test user flows easily.
- Network Testing: It intercepts requests to validate APIs or mock data. This ensures backend features work.
- Visual Checks: Puppeteer captures screenshots and PDFs of pages. Teams verify layouts without manual effort.
- Extra Uses: It monitors performance or scrapes data as needed. Startups gain added value from one tool.
JUnit
It is a lightweight unit testing framework for Java applications, widely used and supported.
- Easy Syntax: JUnit uses annotations to mark tests, keeping things clear. New developers pick it up fast.
- Build Tools: It fits with Maven and Gradle for smooth integration. Startups automate testing in their workflow.
- Flexible Tests: Parameterized tests run with different inputs. Teams check edge cases without extra scripts.
- Assertions: It verifies results with simple checks. Small teams confirm code behavior quickly.
- Extensions: Third-party add-ons expand its features. Startups adapt it to their needs.
TestNG
It is a testing framework inspired by JUnit but with additional features for parallel execution and data-driven testing.
- Test Groups: TestNG organizes tests into categories for better control. Teams manage large suites easily.
- Speed Gain: It runs tests in parallel to finish faster. Startups save time on big projects.
- Data Testing: It uses parameters for varied inputs. Teams test multiple scenarios with one script.
- Detailed Logs: TestNG provides clear reports on results. Small teams track issues without extra tools.
- Web Support: It pairs with Selenium for browser tests. Startups cover more ground efficiently.
TestCafe
It is a Node.js-based tool that doesn’t require WebDriver and works well for modern web apps.
- Browser Ready: TestCafe runs on HTML5 browsers without setup. Teams test anywhere instantly.
- Smart Waits: It waits for page loads and elements automatically. This keeps tests reliable for beginners.
- Language Options: It supports JavaScript, TypeScript, and CoffeeScript. Startups use their preferred tools.
- Concurrent Tests: It runs tests across browsers at once. Teams get results quicker.
- Built-In Runner: It includes a test runner and reports. Small teams avoid extra software.
Nightwatch.js
It is an end-to-end testing tool for websites and web apps, based on Node.js and Selenium.
- Clear Syntax: Nightwatch.js uses simple commands for tests. New team members learn fast.
- Parallel Execution: It runs multiple tests together for speed. Startups handle tight deadlines better.
- Cloud Testing: It connects to cloud testing platforms for wider reach. Teams test on many setups easily.
- Test Runner: A built-in runner manages execution and logs. Small teams stay organized.
- Page Objects: It supports reusable code patterns. Startups maintain tests with less effort.
Cloud testing platforms help startups test across devices without owning them. This saves money and time.
QA Wolf
It is a test automation platform built for teams to reach full test coverage quickly using JavaScript.
- Auto Code: QA Wolf creates test scripts from user actions. Teams save time on writing.
- End-to-End: It tests full app flows from start to finish. Startups ensure everything works.
- CI/CD Link: It fits into continuous integration setups. Teams automate with every update.
- Dashboard: A central view tracks test progress and results. Small teams stay on top.
- Teamwork: It offers features for group collaboration. Startups share testing tasks easily.
Rainforest QA
It combines crowd-sourced manual and no-code automated testing. Great for MVPs and early validation.
- Real Testers: It uses human testers on actual devices. Startups get practical feedback.
- No-Code Tests: Teams build automated tests without coding. Beginners jump in fast.
- Quick Results: It delivers test outcomes in minutes. Small teams move forward swiftly.
- Regression Checks: It catches bugs after updates. Startups maintain quality easily.
- Tool Integration: It connects with project management apps. Teams keep everything aligned.
Ghost Inspector
It is a test automation and monitoring tool with a browser-based UI and recorder.
- Recorder: A Chrome extension captures test steps. Teams create tests without coding.
- Scheduled Runs: It monitors apps with regular tests. Startups spot issues early.
- Alerts: It notifies teams of failures via email or apps. Small teams react fast.
- Data Testing: It uses CSV files for varied inputs. Teams cover more cases.
- App Links: It integrates with Slack and PagerDuty. Startups stay connected.
Leapwork
It is a visual test automation tool with flowchart-based test building, ideal for non-coders.
- Visual Design: Teams build tests with drag-and-drop flows. No coding skills needed.
- Data Use: It pulls from external sources for tests. Startups test real scenarios.
- Reports: It offers clear analytics on test runs. Teams understand results fast.
- Parallel Runs: It executes tests together for speed. Small teams save effort.
- CI/CD Fit: It connects to automated workflows. Startups test with every change.
Conclusion
Startups need tools that save time and deliver quick feedback. Automation testing tools cut down manual work and boost product quality. The options here help teams test fast without slowing development. Many are free or open-source, fitting tight budgets perfectly. This makes them a smart pick for small companies.
Choosing the right tool depends on your team’s skills and project needs. Some focus on web apps, others on mobile or APIs. Think about what your startup builds now and plans for later. A tool that grows with you prevents headaches down the road. Testing early and often keeps customers happy.
Automation testing tools let startups focus on innovation. They handle repetitive tasks so teams can create new features. With these solutions, small companies release better products faster. Pick one that matches your goals and start testing today. Quality matters, and these tools make it achievable.
Automation
Introduction: The AI-Powered Transformation
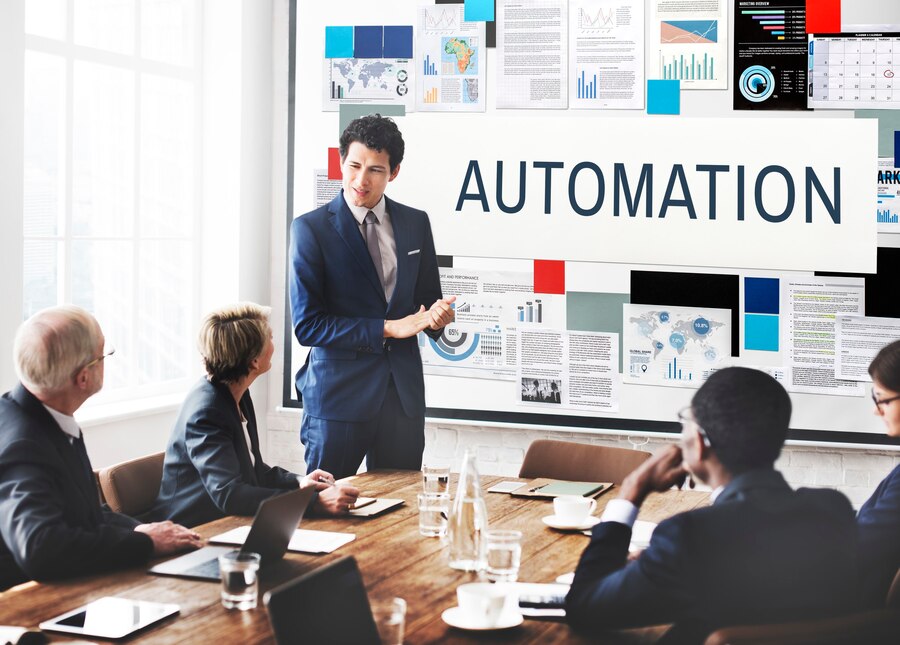
By 2025, AI will accept fundamentally adapted how we actualize content, administer workflows, and collaborate with modern media. The accelerated modernized AI tools—such as Vidnoz AI tool of video language translator — is automating tasks that are already appropriate hours of chiral effort, carrying faster, added efficiency, and higher-quality results.
From AI-generated videos to automatic translations, AI is eliminating repetitive tasks, accepting creators, marketers, and professionals to focus on action and creativity. This commodity explores the addition of beachcomber in agreeable conception and assignment efficiency, highlighting how AI is acceptable as a basal asset in 2025.
1. AI in Content Creation: Faster, Smarter, and More Efficient
Automated Video Production & Editing
Gone are the days of spending hours editing videos. www.vidnoz.com tools now automate:
- Auto-editing – AI trims, enhances, and even suggests the best clips.
- Voiceovers & Dubbing – Tools like video language translator by Vidnoz AI instantly convert speech into multiple languages.
- AI-Generated Thumbnails & Captions – No more manual design work; AI optimizes engagement automatically.
AI Writing Assistants & Content Generation
- Blogs, scripts, and social media posts are now drafted in seconds.
- SEO optimization is handled by AI, improving rankings without manual keyword stuffing.
- Personalized content tailored to audience preferences is generated effortlessly.
AI in Social Media & Marketing
- Automated ad creation – AI designs and tests multiple ad variations in minutes.
- Chatbots & AI-driven customer engagement – Instant responses, personalized recommendations, and 24/7 support.
- Predictive analytics – AI forecasts trends, helping brands stay ahead.
2. AI in the Workplace: The Rise of Automation
AI-Powered Productivity Tools
- Smart scheduling & meeting summaries – AI transcribes and highlights key points.
- Automated data entry & reporting – No more manual spreadsheets; AI extracts insights instantly.
- Virtual assistants – AI handles emails, reminders, and task management.
3. AI Video Language Translator: A Case Study in Efficiency
One standout AI tool leading this revolution is video language translator by Vidnoz AI , which:
Translates videos in real-time – No need for manual subtitling.
Preserves voice tone & emotion – AI ensures natural-sounding dubs.
Supports multiple languages – Perfect for global marketing and education.
This tool exemplifies how AI is cutting production time while improving quality—exactly what modern businesses need.
Conclusion: Embracing the AI-Driven Future
By 2025, AI won’t aloof assist—it will boss workflows, authoritative agreeable conception and business operations faster, smarter, and added cost-effectiveness. The key to success? Adapting aboriginal and leveraging AI accoutrement like AI video accent translator to break ahead.
The future isn’t about replacing humans—it’s about enhancing human potential with AI.
-
GENERAL8 months ago
From Fan Art to Original Works: The Diversity of doujindesu Creations
-
Entertainment4 months ago
Enchantment & Excitement: Crafting Unforgettable Event Experiences
-
GENERAL6 months ago
England Business Visa Requirements for American and International Citizens in 2025: A Guide for Entrepreneurs
-
GENERAL4 months ago
Crossword Conundrum: The Significance of vault opener nyt crossword
-
GENERAL7 months ago
Latest Trends in Men’s and Women’s Jackets for the Upcoming Season
-
GENERAL4 months ago
Exploring the World of nhentai.nef: A Comprehensive Guide for New Users
-
Health8 months ago
Discovering gel ooru: The Ultimate Guide to This Unique Traditional Craft
-
GENERAL9 months ago
Why raterpoint is Revolutionizing Customer Feedback