Manufacturing
Ensuring Quality and Consistency in IND-Enabling Manufacturing
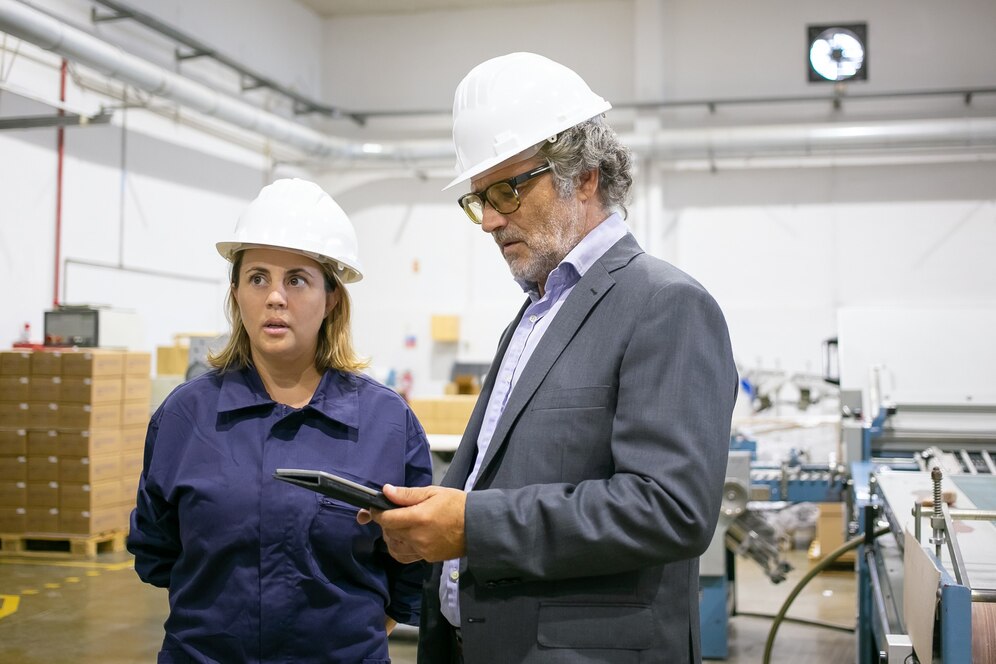
Introduction
The path from drug discovery to market introduction is a long and intricate, requiring rigorous screening and meticulous quality standards to ensure that only the best therapeutic options advance. During the Bioduro-Sundia IND enabling phase, the processes focus on readying a drug candidate for further clinical trials. This preparation is vital, ensuring potential therapies meet safety and efficacy benchmarks to protect public health and maintain trust in pharmaceutical advancements. In the IND enabling stage, manufacturers like Bioduro-Sundia play an essential role in guaranteeing the consistent production of high-quality drug components suitable for testing. Their emphasis on innovation and adherence to regulatory standards ensures that the medicines of tomorrow are safe, effective, and capable of addressing unmet medical needs.
Understanding IND-Enabling Manufacturing
IND-enabling manufacturing is a foundational yet complex phase within drug development, often acting as a precursor to clinical trials. This stage involves establishing robust processes that ensure pharmaceutical products are consistently produced to a predictable standard. By doing so, manufacturers ensure that the subsequent data collected during clinical trials are valid and reliable. The emphasis is on creating a reliable framework that produces drug substances with the necessary quality and consistency at each production stage. This not only aids in generating actionable data for regulatory bodies but also ensures that the drug’s intended effects are rightfully attributed to its intrinsic properties rather than variability in production processes. Such diligence pays dividends in the form of regulatory approvals and streamlined transitions into human trials.
The Role of Quality Control
The centrality of quality control in IND-enabling manufacturing cannot be overstated. It is a multi-layered approach comprising numerous processes designed to fortify drug production’s overall safety and effectiveness. These processes are not just about obtaining satisfactory end products but entail exhaustive testing from ingredient sourcing to final product formulation. Rigorous laboratory assessments, coupled with real-time monitoring, help in identifying potential deviations early. This proactive approach is essential for minimizing errors that could compromise a product’s therapeutic application. Quality control also involves crafting detailed checks and balances that ensure compliance with national and international manufacturing standards, essential for gaining and retaining market access globally. Continuous improvements in these systems reflect an industry commitment to patient safety and product effectiveness, forming the bedrock upon which trust is built.
Ensuring Consistency
Consistency in manufacturing is another pillar that supports successful drug development. Consistency translates into endocrine-like precision in the mass production of pharmaceuticals, ensuring that batch variability is minimized to the greatest extent possible. This standardization is crucial, as it affirms that any observed patient responses are directly tied to the drug’s inherent characteristics and not due to manufacturing variances. To achieve this desired level of consistency, manufacturers adhere to stringent protocols and Standard Operating Procedures (SOPs) that dictate every aspect of production. The rigorous application of these norms ensures that each batch will fulfill specified requirements, attenuating the risk of anomalies that could confound clinical outcomes. This meticulous attention to manufacturing fidelity is essential for advancing clinical trials and securing the final regulatory approvals necessary to bring a new drug to market.
Technological Advancements
The pharmaceutical industry continues to harness the power of technological advancements to optimize IND-enabling manufacturing. These innovations range from automation to big data analytics, each contributing significantly to the precision and efficiency of drug production processes. Automation eliminates much room for human error, ensuring a consistently high-quality product. Meanwhile, big data analytics empowers manufacturers by providing valuable insights into process efficiencies and product outcomes. Technologies such as real-time process monitoring enable swift corrective actions that safeguard product integrity in the face of unexpected deviations. These advancements collectively inform a more adaptable, scalable, and responsive manufacturing environment, paving the way for streamlined production pipelines that are not only more efficient but also more capable of meeting the stringent demands of the pharmaceutical market. Pharmaceutical manufacturers leveraging these innovations report improved production workflows and the ability to better adapt to the growing complexity of today’s drug demands.
Regulatory Compliance
Regulatory compliance serves as the custodian of quality in IND-enabling manufacturing. Under stringent guidelines set forth by global regulatory bodies like the FDA, manufacturers must meticulously document and validate each facet of their manufacturing processes. This compliance is vital in ensuring drug products meet the rigorous safety and efficacy standards required to protect patients. A comprehensive understanding of regulatory expectations facilitates seamless interactions with oversight bodies but also assists in minimizing the risk of costly setbacks during drug approval processes. By staying updated on regulatory shifts and innovations, manufacturers can foster a culture steeped in continuous improvement, offering quality assuredness that satisfies regulators and healthcare providers alike. This proactive compliance strategy is a linchpin in avoiding deficiencies during regulatory reviews, allowing for a smoother and more efficient path toward market introduction. Compliance insights enable companies to manage risk effectively while maintaining the utmost quality standards.
The Impact of Ensuring Quality and Consistency
The emphasis on quality and consistency in IND-enabling manufacturing has extensive implications for the entire drug development ecosystem. When manufacturers adhere to rigorous quality control and operational consistency principles, they lay the groundwork for robust clinical data that is pivotal for regulatory approval. High-quality, reliable drug products lead to more consistent clinical trial outcomes, reinforcing the claims of safety and efficacy that new therapeutics rely upon. This proactive approach to quality assurance accelerates the path to market entry, bringing forth a new era of therapeutics capable of improving global health outcomes. This enhances trust among regulators, healthcare providers, and patients. Thus, the commitment to quality and consistency is not merely a procedural or regulatory obligation but a strategic advantage that maximizes the potential success of therapeutic interventions to address unmet medical needs.
Conclusion
As the pharmaceutical industry navigates the increasing complexity of modern drug development, the necessity for unyielding quality and consistency in IND-enabling manufacturing becomes evident. Organizations like Bioduro-Sundia are pioneering this movement with precision scientific methods, comprehensive quality control measures, and an unwavering commitment to regulatory compliance. The adoption and integration of advanced technological solutions ensure that the process of bringing innovative therapies to market is efficient and aligned with the highest standards of safety and efficacy. This focused effort ensures new insights transition from the lab to the clinic with optimal predictability and patient benefit, emphasizing a worldwide commitment to improving health outcomes and advancing medical care.
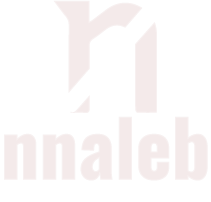
-
GENERAL7 months ago
From Fan Art to Original Works: The Diversity of doujindesu Creations
-
Entertainment3 months ago
Enchantment & Excitement: Crafting Unforgettable Event Experiences
-
GENERAL5 months ago
England Business Visa Requirements for American and International Citizens in 2025: A Guide for Entrepreneurs
-
GENERAL3 months ago
Crossword Conundrum: The Significance of vault opener nyt crossword
-
GENERAL6 months ago
Latest Trends in Men’s and Women’s Jackets for the Upcoming Season
-
GENERAL3 months ago
Exploring the World of nhentai.nef: A Comprehensive Guide for New Users
-
Health7 months ago
Discovering gel ooru: The Ultimate Guide to This Unique Traditional Craft
-
GENERAL8 months ago
Why raterpoint is Revolutionizing Customer Feedback